What rotates 20 times per second and pushes through 50 kilometres of paper an hour? Impressively fast: a roller in a rotary offset printing machine. The machine fills an entire hall and is a cornerstone of print shops. Cardboard packaging, catalogues and brochures pass through everyone’s hands on a regular basis. And this is how they are produced…
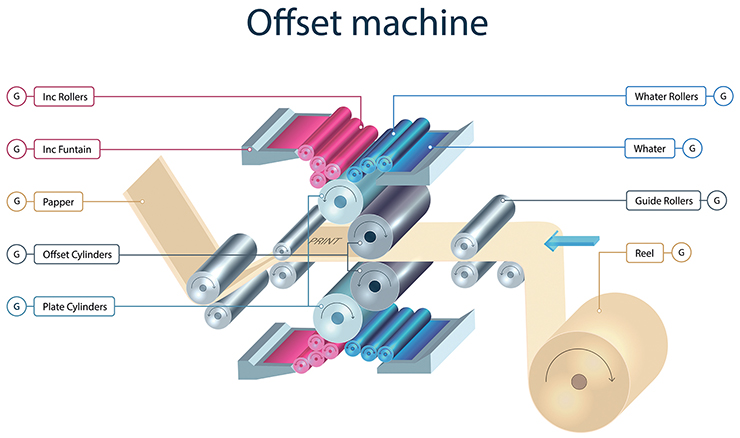
Printing towers as high as the hall ceiling, a single machine up to 20 m long, photo-exposed printing plates and 20-km-long paper rolls weighing up to 6 t. This is followed by automated systems for cutting, folding, stitching, gluing or binding as well as robots that sort and pack the printed materials. The printing process of newspapers, flyers and the like is full of fascinating technology. If you are curious, you can take a look at a rotary offset printing machine in a 3D tour of an Italian print shop, learn more about its functions and even look inside it virtually.
Technology plays an important role
Rotary offset printing is the combination of two printing processes: rotary printing and offset printing. Rotary presses were in use as far back as the beginning of the industrial revolution. Their advantage is that they can print simultaneously on both sides of a continuous paper web by using reels (i.e. rotation), which is much quicker than printing single sheets. Offset printing is the most common technique used to print glossy products such as magazines, catalogues and brochures. It is an indirect printing process in which the print roll and printing plate do not come into direct contact with the material being printed.
Offset printing is based on the principle of the repulsion of water and oil. The printing plate is produced by photo exposure in such a way that the non-printing areas are hydrophilic. This manufacturing process is simple and inexpensive. Each colour (CMYK: cyan, magenta, yellow, black) requires its own printing plate and thus a separate printing unit. The printing plate is first wetted by water rollers in the dampening system and then ink is applied by ink rollers in the inking system. The ink-water mixture is then applied to the paper by the rubber-coated offset roller (see image below).
Hot and dry, cool and glossy
The printed but still wet paper web then runs horizontally through a dryer and is dried at temperatures of up to 250°C (heat-set process). The paper is then cooled again in the cooling unit. The lost moisture is returned to the paper by applying a silicone and water emulsion during the web rewetting process. This hardens the inks, gives the print product its typical gloss and improves scratch resistance – indispensable for high-quality print products.
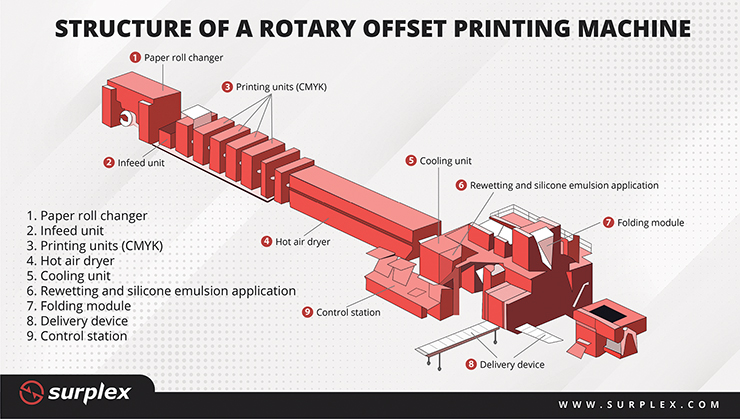
Final processing: cutting, folding, packing
In the folder unit, the 2m-wide and 20km-long paper web is cut, stacked, folded, cut again, laid and folded until the desired format is achieved. The folded sheets are also glued, pasted or stapled as necessary. They can also be perforated. With the help of a robot arm, the finished print products are removed from the rotary offset printing machine, stacked and finally packaged.
Those presumed dead live longer
The end of the printing industry is frequently predicted, but the reality is different. Many still prefer to read long journalistic articles, leaflets or shop brochures in hard copy and more and more companies are turning to paper-based packaging. Paper accounted for over 40% of all packaging in the EU in 2019. The trend is upward as paper is sustainable and recyclable.
Investing in rotary offset printing
The UE printing sector comprises about 120,000 companies employing approximately 770,000 people. They generate annual turnover of around 88 billion euros. For print shops to remain competitive in the dynamic sales market, investments have to be made within a tight budget. A short depreciation period means lower risk. This can be achieved by buying second-hand machines as they are much cheaper than new ones and will last for many years to come if properly maintained.
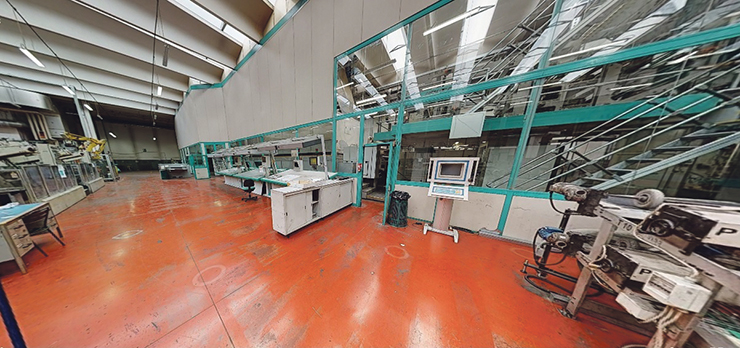
The Surplex.com industrial auction house for used machinery and factory equipment currently has three complete production lines available for direct purchase: 3 Manroland rotary offset printing presses in the 16, 48 and 64-page size classes plus all the associated finishing units, control stations and robot technology. The digital transition is well underway, not only in the printing industry but also in the machine trade: Surplex combines traditional auction business with online business. One aspect of the digital side of things involves 3D tours of entire factory halls, bringing interested parties from all over the world right to the machines and creating maximum transparency.
About Surplex
Surplex is one of Europe’s leading industrial auction houses and trades worldwide in used machines and factory equipment. The 16-language Surplex.com auction platform is visited around 50 million times every year. We sell more than 55,000 industrial products per year in over 500 online auctions. The company is based in Düsseldorf and has offices in 15 European countries. Over 200 employees from 20 different nations generate an annual turnover of more than 100 million euros.
Related links
Offset Printing
Surplex.com
3D Tour