The Rebel EMP 215ic welder for MIG/MAG, MMA and TIG welding offers primary power and location flexibility and some of the most innovative welding technology available today. It provides a true multi-process arc performance, location flexibility, lightweight portability and a groundbreaking operator interface with LCD/TFT display.
A unique sMIG (‘smart MIG’) function, enables users to begin MIG welding – with an extremely stable arc – simply by setting metal thickness and wire diameter. Unlike competitive units, there is no need to enter information for shielding gas mix. It is optimised for light fabrication, repair and maintenance, automotive bodies, HVAC, farm equipment repairs and training schools.
Rebel can also weld with flux cored wire and MMA electrodes up to 4 mm, making it perfect for small fabrication shops, construction sites and mechanical contractors, particularly where it makes sense to run short welds with a portable machine and finish the length of the weld with a stationary unit.
Rebel welders appeals to operators because they are the most powerful, portable single-phase units on the market. Rebel enables users to be more productive, as well as improve results with their best-of-class arc performance. Its true multi-process arc performance eliminates the need to purchase separate welders for MIG welding and MMA/TIG welding, making it the best value on the market.
Smart phone functionality
Operators interact with the Rebel EMP 215ic using a unique control that combines traditional weld parameter adjustments with the functionality of a smart phone (in fact, the 110mm colour display uses the same thin-film transistor (TFT) LCD technology found in smart phones). No other welder combines this level of simplicity, performance and control. The TFT user interface offers in 21 languages (covering all of Europe), offering important information beyond weld parameters, such as part numbers for easy reordering.
When connected to 230V primary, the unit provides a MIG output of 20 to 220 amps, a Stick output of 30 to 160 amps and a TIG output of 5 to 240 amps. When connected to 120V primary, the unit provides a MIG output of 15 to 130 amps, a Stick output of 5 to 110 amps and a TIG output of 5 to 140 amps.
Rebel EMP 215ic accepts 100 and 200mm wire spools, runs 0.6 to 1.2mm diameter wires. It weighs 18kg, measures 584 x 229 x 406mm and features a five-handle roll cage and unibody construction that integrates the front, back and top panels to provide superior durability for protecting internal components.
The unit comes ready-to-weld with a professional-grade MIG torch, MMA electrode holder, drive rolls, contact tips, all required hoses and cables and a spool of ESAB´s innovative, non-copper-coated wire AristoRod 12.50 wire.
Robust Feed U82 wire feeder offers unmatched combination of advanced process controls and extreme durability
Robust Feed also offers Red Dot Award-winning ergonomics and usability
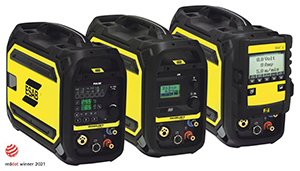
ESAB has launched the Robust Feed U82 wire feeder, which includes a full suite of advanced process control functions that help users increase competitiveness through consistent weld quality and appearance, address workforce skill issues, improve productivity and reduce operating costs through more uptime. The feeder accepts 200 and 300mm wire spools and is designed to work with ESAB’s Aristo® 500ix and Aristo Mig 4004i Pulse power sources for MIG/MAG, pulsed MIG, flux cored and TIG welding, as well as carbon arc gouging.
The Robust Feed U82 combines the extreme durability of a portable, enclosed feeder and the precision wire feeding and control of a shop-style feeder. Its PreciDrive wire drive system delivers better arc starts and stops without backlash or play in the gears and features a 4-wheel drive system. Large diameter (38mm) drive rolls offer more gripping area and provide more pushing force without deforming soft cored and aluminium wires, a common source of feeding problems. It handles solid wires up to 2.0mm and cored wires up to 2.4mm and feeds wire at speeds of 0.8 to 25.0m/min.
“With the introduction of the Robust Feed U82, which offers our most advanced control panel, users in every industry can take advantage of the unique productivity, reliability and durability benefits of Robust Feed,” says Arne Lagerkvist, Global Product Manager – Heavy Industrial Welding Equipment, ESAB. “This feeder also offers ESAB’s exclusive SuperPulse modified pulsed spray transfer process. SuperPulse combines a conventional pulsed waveform and with a second waveform or process to achieve specific goals when welding aluminium or stainless steel.”
SuperPulse process combinations include:
- Pulsed MIG/short arc transfer, which provides maximum control over heat input when welding thin sections and for root-pass welding.
- Pulsed MIG/pulsed MIG, designed for welding material from 1.6mm and thicker with great control over heat input, bead profile, bead appearance and travel speed.
- Spray arc transfer/pulsed MIG, which delivers higher productivity on thicker sections while still preserving the ability to weld vertical-up without any weaving motion, which reduces operator fatigue.
Ultimate control
Robust Feed U82 enables users to set limits on voltage and amperage, ensuring that operators can’t step outside of a set welding procedure. Further, once weld parameters have been set, the control can be locked, preventing unauthorised personnel from changing them. Additional quality functions include storing data on the last 99 welds, monitoring production statistics such as arc-on time and quantity of wire consumed and exporting statistics and procedures using a USB connection.
Robust Feed U82 enables users to create custom synergic lines or to choose from 259 factory-programmed synergic lines for steel, stainless steel, aluminium and NiCrMo alloys using the MIG, pulsed MIG or SuperPulse™ processes. Preprogrammed synergic lines speed set up because they have optimised parameters for the wire type, wire diameter, shielding gas and process selected. Data associated with each synergic line can be fine-tuned and subsequently stored, and the U82 can store up to 255 welding schedules.
Synergic lines for pulsed MIG can save many hours of process development time. To begin pulsed welding, operators simply select the synergic line. The system then provides optimum dynamic arc control to maintain consistent penetration and weld bead appearance, automatically adjusting for variations in arc length and wire feed speed. If needed, operators can use the wire feed speed control to fine tune the arc and all pulsing parameters will be automatically adjusted.
Robust Feed U82 offers all standard controls, as well as Qset and Short Circuit Termination (SCT). Qset — or quick set — automatically optimises the short circuit arc for the gas/wire combination installed. After a few seconds of welding, the system adapts welding parameters to match an operator’s individual welding style, notably compensating for variations in contact tip to work distance and torch angle (such as when operators manoeuvre the torch around corners). This lets the operator focus on torch mechanics instead of worrying about whether they have set proper parameters. SCT technology sharpens the end of the solid MIG wire at the termination of a weld to promote a positive next arc start, reduce spatter and reduce the possibility of cold lap. SCT technology also eliminates the need for the operator to clip the wire.
The Robust Feed U82 includes a 50 mm dinse connection on the back for the MMA or gouging torch and, when paired with an Aristo 500ix power source, allows operators to select the gouging mode at the feeder, eliminating the need to return to the power source to set process mode or switch cables for gouging. In addition, the Aristo/Robust Feed U82 combination gouges using a CV output. CV provides smoother gouging performance because the system will adjust the output current to maintain a set voltage even as the distance between the carbon and workpiece varies.
Award winning
Robust Feed, which won the prestigious Red Dot Award for product design, improves ergonomics. When carried by the middle handle, it rests comfortably against the side of the operator’s body when walking longer distances. Closer to the point of welding, additional front and rear handles make it easy to carry up a ladder, manoeuvre through confined spaces or pass the unit from one person to another.
The Robust Feed U82 offers an IP23 models protection class rating (other models offer an IP44 rating). A completely-sealed wire feed compartment protects the wire from water splashes, dust and other contaminants. An optional heater inside the wire feed compartment drives off moisture to preserve wire integrity, and double-wall design has special zones to provide impact and abrasion resistance. The controls, power and gas cable connections are protected inside the housing, and a reliable strain relief removes cable stress.
The Robust Feed series also includes the Robust Feed Pro, Robust Feed Pulse and Robust Feed U6 models. Target markets include traditional portable feeder applications in the ship, boat, civil construction, offshore, railcar and heavy maintenance industries, as well as users in structural steel, tank, vessel, trailer, mobile equipment and general fabrication.
“Between grinding dust, dirt and physical abuse, workshop environments can be extremely demanding,” says Lagerkvist. “The durability of Robust Feed can improve uptime in all applications, while its PreciDrive wire drive system maintains precision wire feeding performance to promote consistent weld quality.”